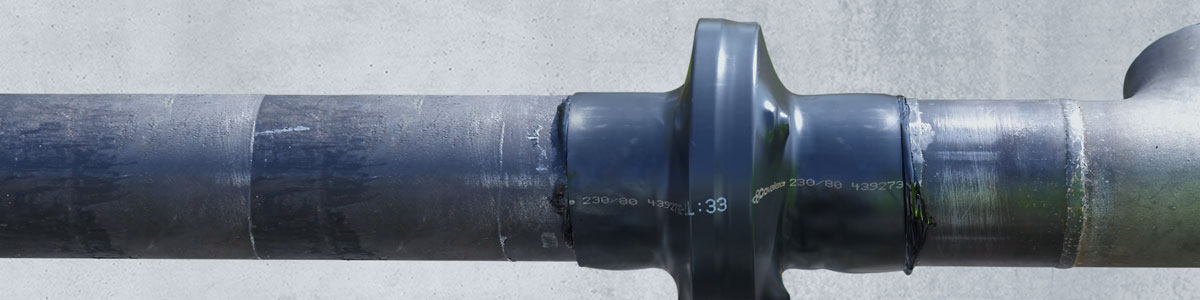
For the subsequent corrosion protection of
buried pipelines
Covalence®
Heat Shrink Products
Type selection
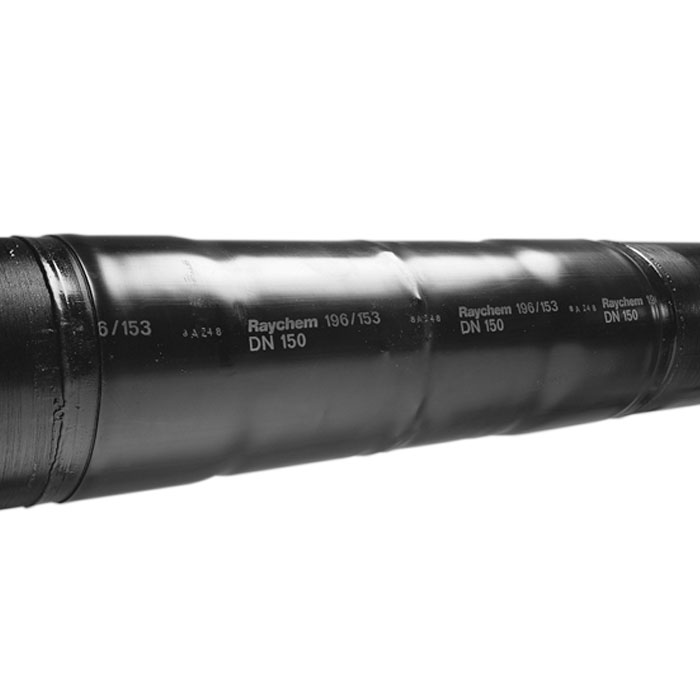
Covalence® CPSM-C30
Covalence® TPSM-C30
Fields of application
For retrocoating of a weld seam, coupling or bolt connection in the fields of new installations
Material
HDPE with viscoelastic mastic sealant
Properties
High shrinking; load class C30;
welded seam:
CPSM-C30 ND 25 - 65, width 500 mm, shrink rate approx. 66%;
TPSM-C30 ND 80 - 200, width 450 mm, shrink rate approx. 36%;
coupling/bolt connection:
CPSM-C30 ND 20 - 125, width 1000 mm, shrink rate approx. 66%
Sizes
Heat shrink sleeve for weld seam: ND 25 - 200;
heat shrink sleeve forcoupling/bolt connection: ND 20 - 125
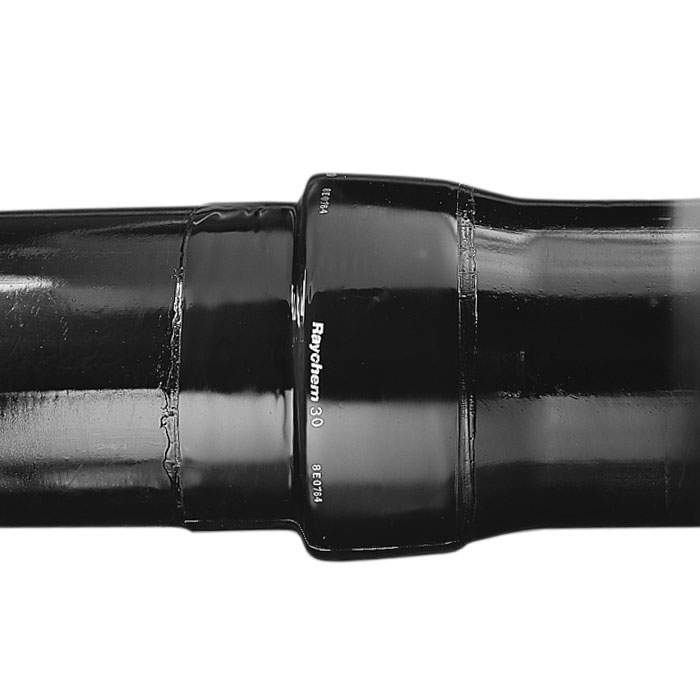
Covalence® MPSM-C30-UNIV-300
Fields of application
For retrocoating of a socket/connection sleeve, mainly at new installations
Material
HDPE with viscoelastic adhesive
Properties
High shrink; load class C30 M; width 300 mm;
shrinkage rate:
approx. 65% ND 80 - 100;
approx. 50% ND 125 - 150;
approx. 45% ND 200 - 250;
approx. 40% ND 300;
approx. 35% ND 350 - 400
Sizes
Heat shrink sleeve for ND 80 - 400
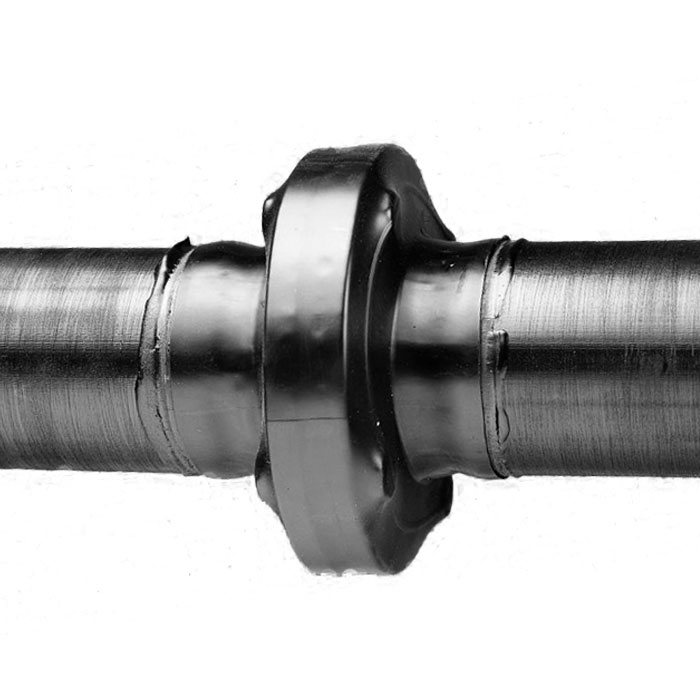
Covalence® FCTS
Fields of application
For retrocoating of flange connections at new installations
Material
HDPE with viscoelastic sealant; adhesive-free flange area
Properties
High shrinking; load class C30; width 300 mm;
shrink rate:
approx. 67% ND 80 - 100;
approx. 45% ND 150 - 200
Sizes
Heat shrink sleeve for ND 80 - 200
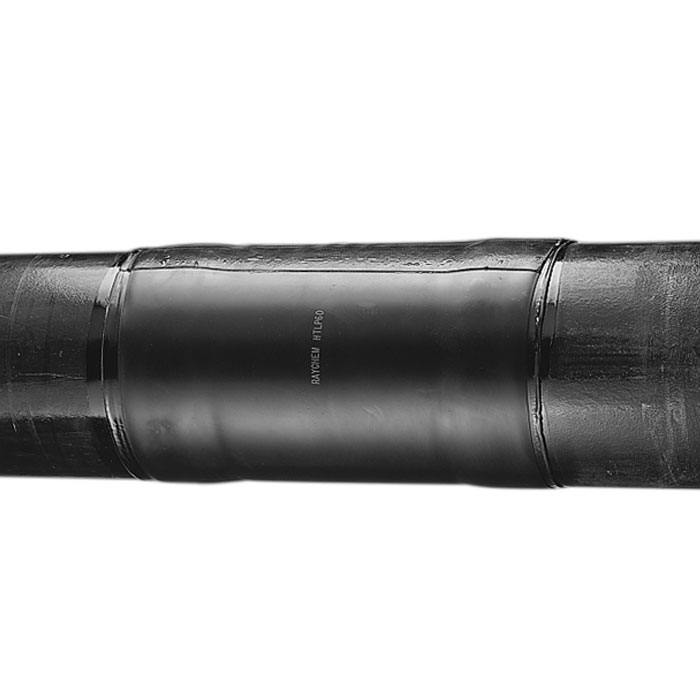
Covalence® WPC-C30-E
Covalence® HTLP60-DCS-C50
Fields of application
For weld seam retrocoating on already laid and
connected pipes or new installations
Material
WPC: HDPE with viscoelastic sealant adhesive;
HTLP60: HDPE with hot melt adhesive
Properties
Stress class C30 (WPC) & C 50 UV (HTLP60); width 450 mm;
shrink rate approx. 25%; available pre-assembled or as roll material
Sizes
Heat shrink sleeve for ND 80 - 1200;
sealing tape:
ND 80 - 450: Width 100 mm;
ND 500 - 1200: Width 150 mm
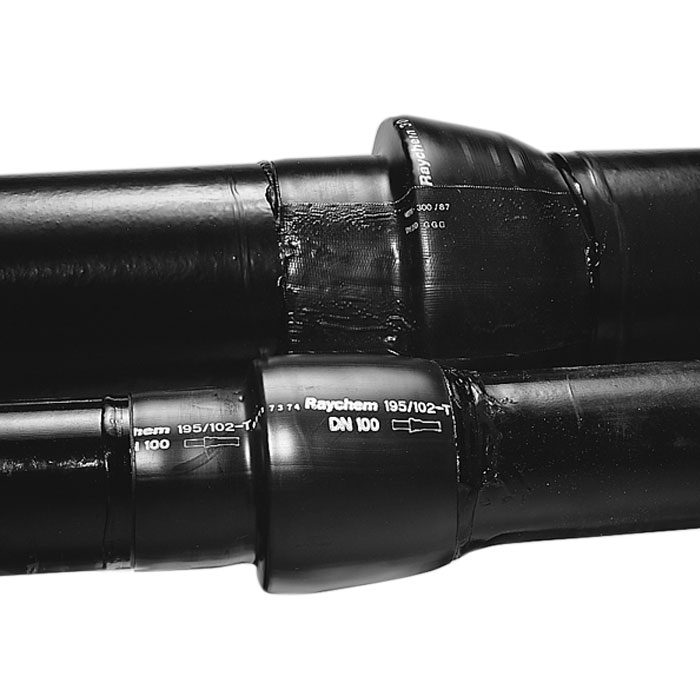
Covalence® MEPS-C30
Fields of application
Heat shrink sleeve for retrocoating a connection sleeve
(MEPS-C30) or a flange joint (FCWS-F, HEPS-C30, MEPS-C30)
Material
HDPE with viscoelastic adhesive with separate sealing tape
Properties
Load class C30; width 300 - 600 mm; shrink rate approx. 36%;
pre-assembled or as roll material
Sizes
Heat shrink sleeve for ND 125 - 1000;
sealing tape up to ND 500: Width 150 mm;
from ND 600: Width 200 mm
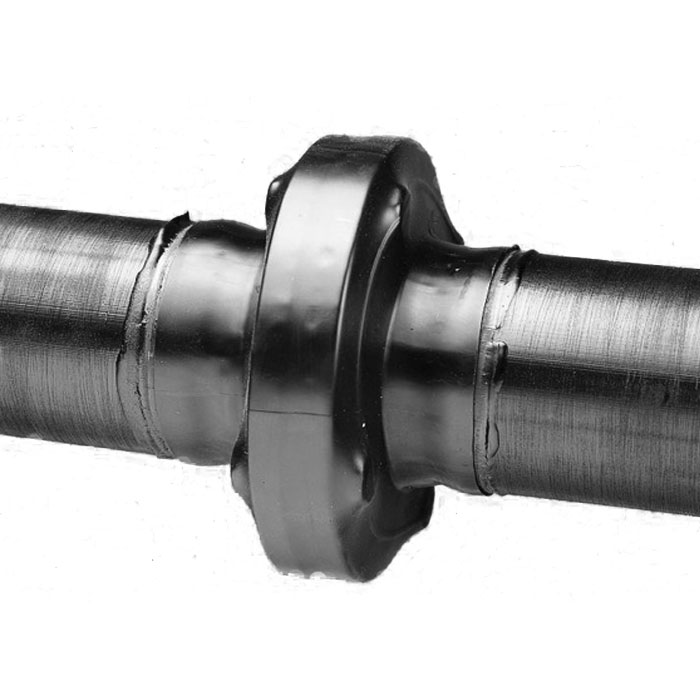
Covalence® FCWS-F
Covalence® HEPS-C30
Covalence® MEPS-C30
Fields of application
For retrocoating of flange connections on already laid and connected pipes or new installations
Material
HDPE with viscoelastic sealant with separate sealing tape;
FCWS-F reinforced material; with zip fastener
Properties
FCWS-F: Load class C30; width 220 - 300 mm; shrink rate approx. 50%;
MEPS-C30/HEPS-C30: Width 450 or 600 mm; shrink rate approx. 36%
(MEPS-C30) and 45% (HEPS-C30); pre-assembled; available as rolls
Sizes
Heat shrink sleeve for ND 50 - 1200 PN 16 (others on request)
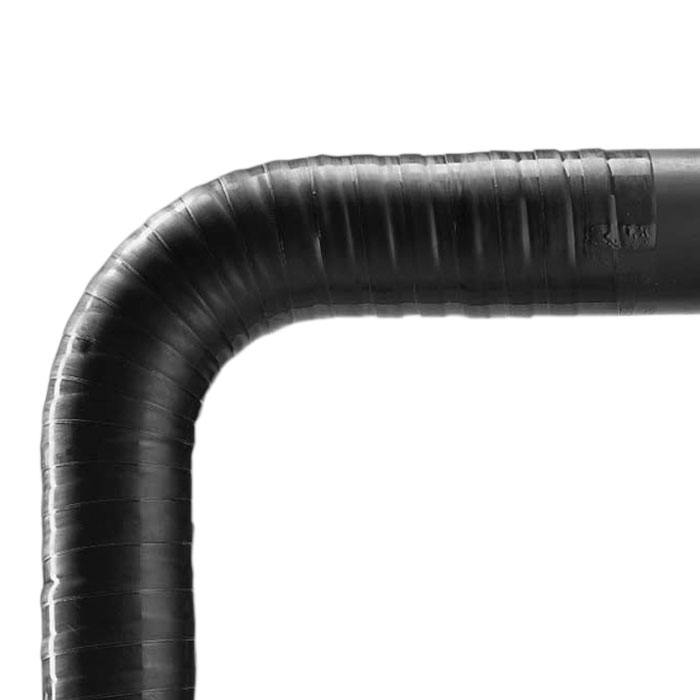
Covalence® FLEXCLAD II
Fields of application
For pipe bend retrocoating, on already laid and connected pipes or new installations
Material
HDPE with hot melt adhesive coating
Properties
Load class C30; Width: 35, 50, 70, 100 mm; shrink rate approx. 20%; roll material
Sizes
Shrinking tape for ND 25 - 300
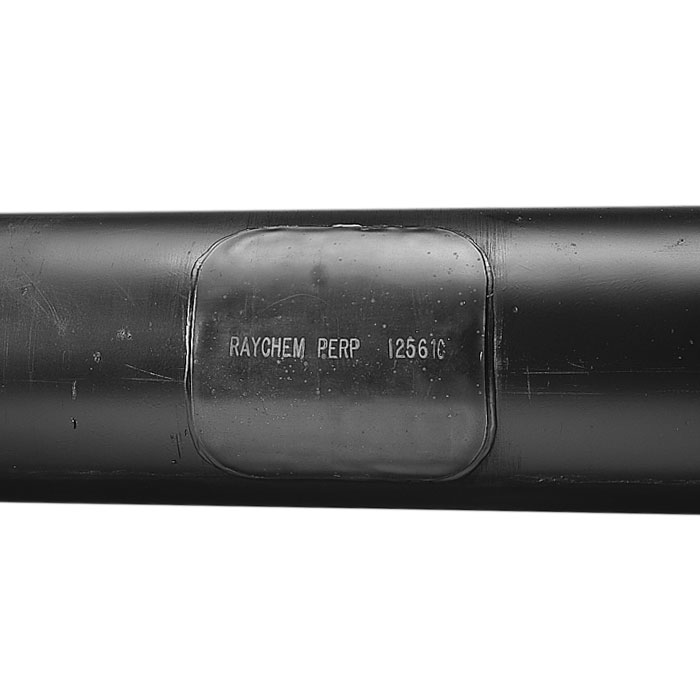
Covalence® PERP
Fields of application
Repair of small damages on the factory coating or coating of welding electrodes
Material
HDPE with hot melt adhesive coating
Properties
Assembled kit or roll material
Sizes
Repair patch 140 x 170 mm incl. filler and emery cloth;
repair patch on rolls 10 m x 450 mm;
Repair filler 50 x 3 mm x 3 mm;
PE-melt stick Ø 25 mm x 305 mm
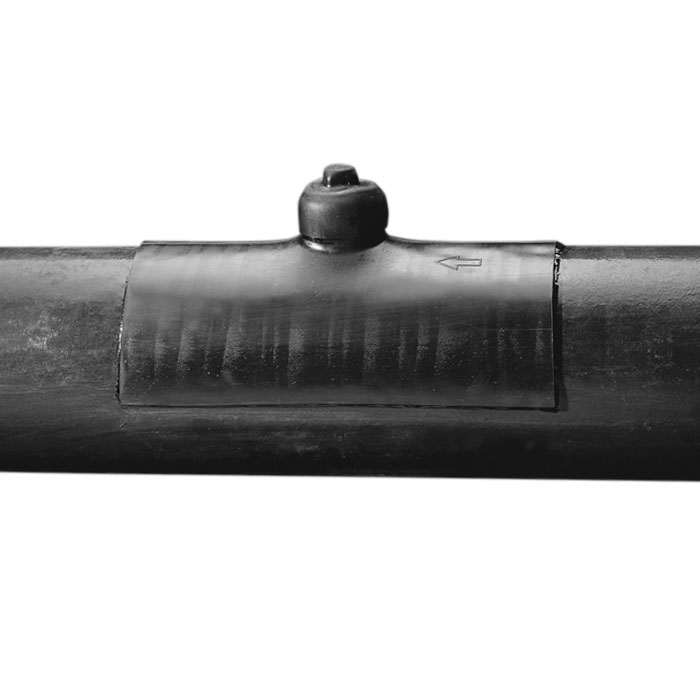
Covalence® BLOT
Fields of application
For subsequent coating of a weld-on socket in fields of gas distribution networks
Material
HDPE as saddle with collar, as well as a separate cap; hot-melt adhesive coating inside
Properties
Load class C 50; saddle 300 x 320 mm; collar approx. 30 - 40 mm
Sizes
Heat shrink molded part 200, 300, 400
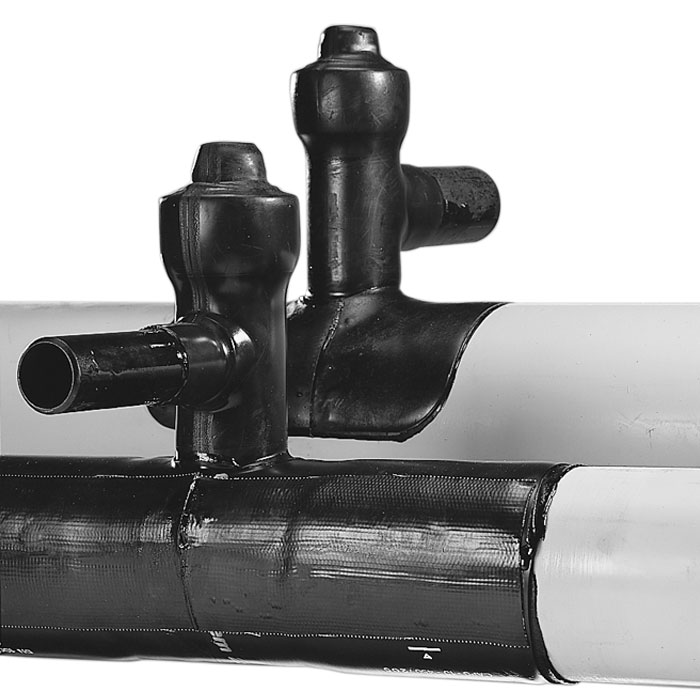
Covalence® HTTE
Fields of application
For subsequent coating of house connection valves
Material
HDPE with special adhesive coating inside
Properties
The thick-walled, strongly expanded molded part is coated with a special adhesive inside; this melts during assembly and leads to a high-strength connection of the shrink molded part with the valve; DVGW certified according to DIN 30672 and DIN EN 12068, load class C50
Sizes
Valve ND 25 - 50
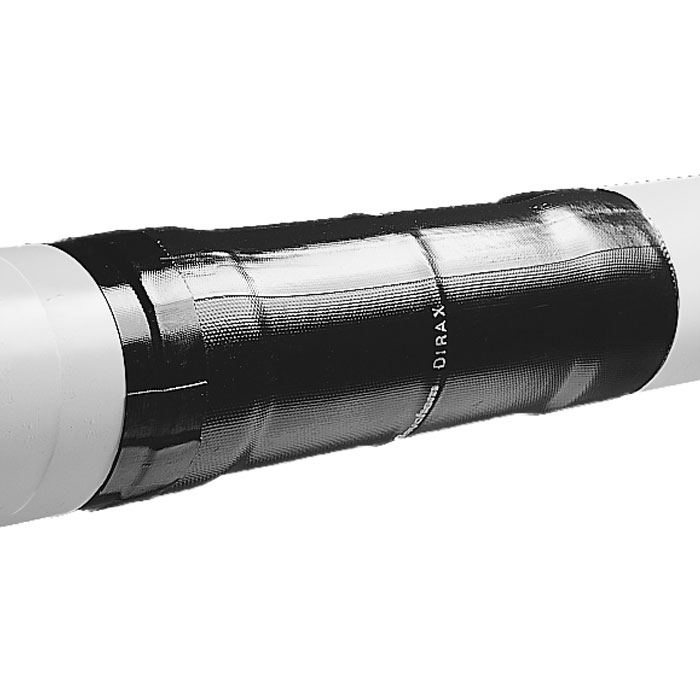
Covalence® DIRAX System
Fields of application
For recoating a circumferential weld seam. For use with increased mechanical requirements.
Material
Fiberglass reinforced polyethylene; copolymer adhesive; two-component epoxy resin
Properties
DIN EN 12068 / DIN 30672; load class C HT 60 UV
Sizes
ND 80 – ND 1850
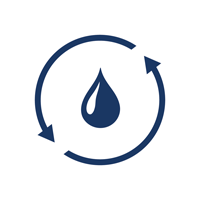
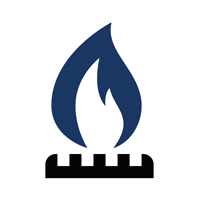
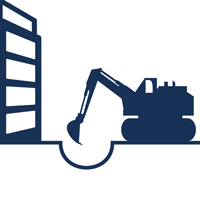
Download
Product Information
Properties
- Backing material made of infusible, heat shrinkable bonded polyolefin
- Coating with hot-melt adhesive, high adhesion, moisture-proof, impact- and abrasion-resistant material, remains flexible and free of cracks even under continuous stress
- Quick and easy installation by shrinking on with gentle propane gas flame without additional adhesive or primer
- Provides protection against creepage, rotting and UV resistant
- Compatible with all common pipeline coatings
- Low preheat requirements, self-healing effect due to viscoelastic sealant
- Dimpled structure in the backing material as an installation aid
Fields of application
Subsequent coating of:
- Welded seams
- Connecting sockets (type Tyton, Fuchs etc.)
- Couplings, bolt connections and pipe bends
- Flanges
- Damaged factory coatings
- Welding electrodes
- Weld seams with higher mechanical load
Sealing of:
- Casing pipes
- Vitrified clay pipes
- Packed and bolt gland sockets
Description
Application: Under normal conditions, no primer is required for heat shrink products. As with all corrosion protection systems, the surface to be coated or subsequently insulated must be clean, free of grease, and dry. With heat-shrinkable corrosion protection systems, it is particularly important to pay attention to compliance with the specified pre-heating temperatures. The more precisely the pre-heating temperatures are kept to, the better and longer lasting the peel and shear resistances of the hotmelt adhesives will be.
The hot melt adhesive liquifies during the shrink process onto the pipe (using a propane gas flame).
The liquefied hot melt adhesive then completely moistens the surface to be coated or subsequently insulated, sticking in any unevenness and fills any small cavities (e.g. transition from steel to factory coating or edges of welded seam). This process is supported by the shrink tension in the retainer material which occurs during processing.
The shrinkage stress of the backing which is in the retainer material is permanently present, and the adhesion of the hot-melt adhesive fix the shrinking tube or the shrink sleeve in place, even if the pipe moves and if there are active shearing forces at the given point.
The backing material, which solidifies after cooling, offers the relatively soft hot-melt adhesive optimal mechanical protection.
DIRAX System
The DIRAX system is a wrap-around heat-shrinkable sleeve reinforced with fiberglass. DIRAX is designed to protect girth welds against corrosion and is the optimum joint protection for PE and FBE coated pipes used in Horizontal Directional Drilling (HDD-Pull Through) applications. The reinforcement gives the backing greater wear resistance.
Construction: Three-layer system
- First layer: Liquid epoxy, solvent-free two-component.
- Second layer: High shear strength copolymer adhesive.
- Third layer: Thick, fiberglass reinforced, radiation cross-linked polyethylene.
- Additional component: Wear Cone as extra protection against pull-through forces, of the same construction as the main sleeve.
Notes
During installation, the epoxy resin is applied to the prepared pipe surface and the heat-shrinkable sleeve is immediately wrapped around the joint on the wet epoxy resin.
The sleeve is then heated and shrunk so that it tightly encloses the joint. During the curing process, the epoxy resin forms strong mechanical and chemical bonds with the pipe surface and the copolymer adhesive layer.
The radiation-cured outer layer forms a robust barrier against mechanical damage and moisture transfer.
Technical Information
A non-destructive, optical quality control is possible:
- The heat shrink product must be completely smooth and bubble-free
- The hot-melt adhesive must have been pressed out at the edges all around the circumference of the pipe
- The required overlap to the factory coating must be at least 50 mm on both sides
- The factory-applied dimpled structure in the backing material (PCI) is no longer visible
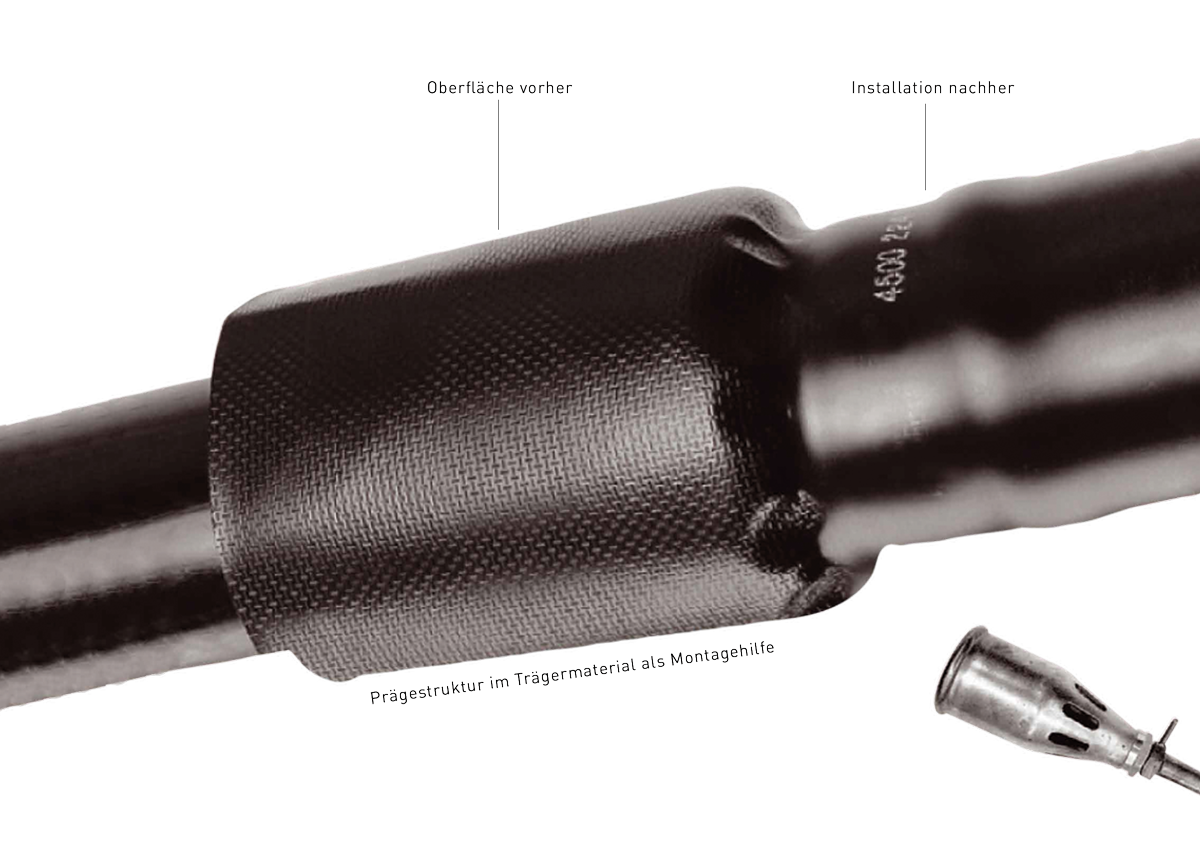
Suitable Accessories
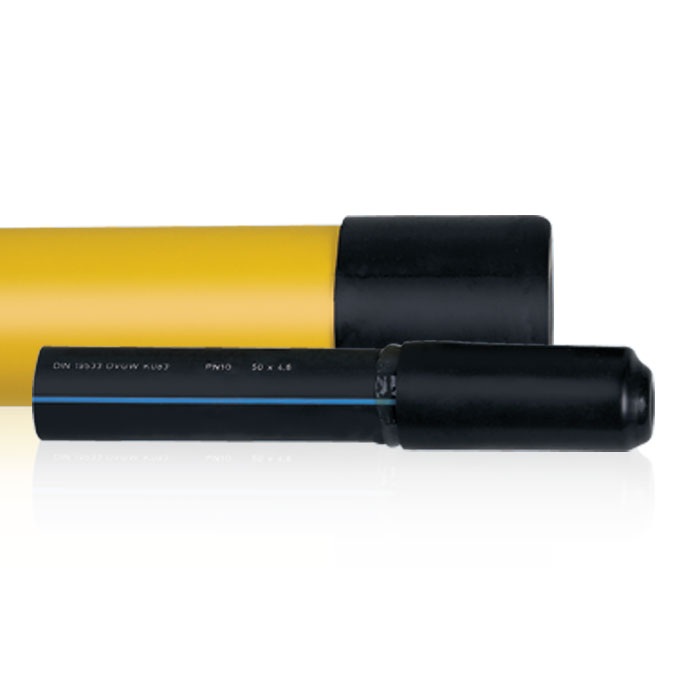
Certificates
To offer our customers the best possible quality and service, we are organized according to DIN EN ISO 9001:2015 and have this continuously checked and certified.
CERTIFICATE ISO 9001:2015
This certification documents our conformity of the quality management system.
AEO-CERTIFICATE
Authorized Economic Operator "AEOC (customs simplification)"
Covalence®

DVGW TYPE EXAMINATION CERTIFICATE; DIN 30672, DIN EN 12068
- CPSM; C 30
- TPSM; C 30
- MPSM; C 30 M
- FCTS; C 30
- WPC C30-E; C 30
- HTLP 60; C 50 UV
- MEPS C30-E; C 30
- HEPS C30-E; C 30
- Flexclad II; C 30
- BLOT; C 50
- HTTE; C 50
- DIRAX; CHT 60 UV